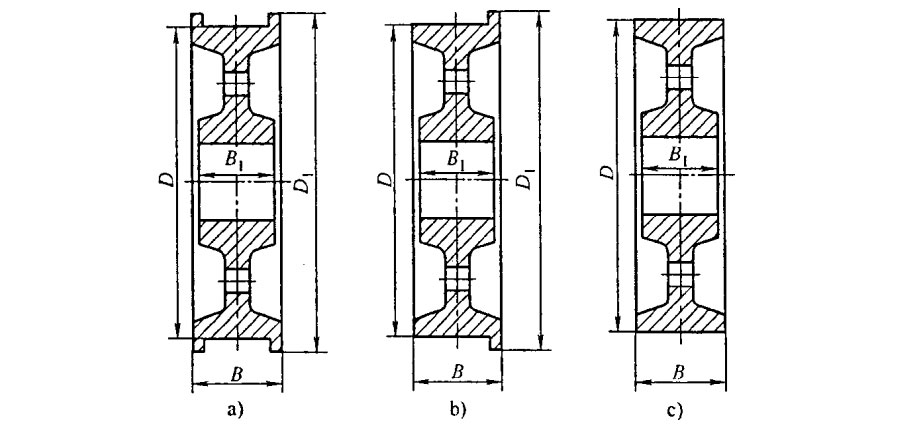
D |
D₁ |
B |
B₁ |
100 |
130 |
80~100 |
95~100 |
125 |
140 |
80~100 |
95~100 |
160 |
190 |
90~100 |
95~100 |
200 |
230 |
95~100 |
95~100 |
250 |
280 |
95~140 |
95~140 |
315 |
350 |
95~210 |
95~210 |
400 |
440 |
105 ~210 |
105 210 |
500 |
540 |
105 210 |
105 210 |
630 |
680 |
120-210 |
120-210 |
710 |
760 |
140 210 |
140~210 |
800 |
850 |
140 210 |
140 210 |
900 |
950 |
145~220 |
140~220 |
1000 |
1060 |
145~220 |
140~220 |
(1250) |
1310 |
145~220 |
140~220 |
Material selection: High-quality steel, such as forged or cast steel, is often used for its durability and ability to withstand wear and tear.
Heat treatment: Crane wheels undergo heat treatment processes, such as quenching and tempering, to enhance their hardness, strength, and resistance to wear and fatigue.
Surface hardening: Methods like induction hardening can be used to create a hard, wear-resistant surface layer on the wheel, extending its service life.
Lubrication: Proper lubrication is crucial to reducing friction, wear, and the generation of heat in the wheel and rail interface. Some crane wheels use self-lubricating materials, while others require regular application of lubricant.
When selecting crane wheels, it’s essential to consider factors such as the crane’s capacity, application, and operating environment. The right combination of wheel type, material, and technology will ensure the crane operates efficiently and safely over its service life.